脱炭素社会の実現に向けた取り組みが急速に広まる中、当社では太陽光発電の自家消費こそ、最良・最速の手段だと捉えています。そのためには、これまで太陽光発電設備が設置されていなかった場所への大量導入が不可欠です。陸屋根用の置き基礎架台「UNIFIX(ユニフィックス)」は、そのような潮流の中で誕生しました。
陸屋根とは傾斜がないフラットな屋根のこと。屋根には建物内への雨水浸透を防止するための防水層が施工されており、屋根に穴を開け太陽光発電設備を設置すると、雨漏りのリスクが生じやすくなります。しかし陸屋根は、工場やスーパーマーケットなどの施設に多く採用されており、自家消費型太陽光発電の推進のためには、必ず押さえるべき課題でした。
01
低重心置基礎架台
UNIFIX〈ユニフィックス〉
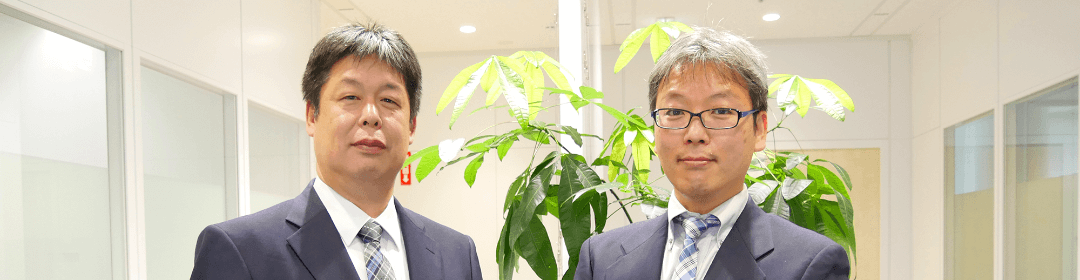
-
S.M
製品開発課 課長 -
D.N
製品開発課 担当課長
満足のいく
陸屋根用架台を
求めて
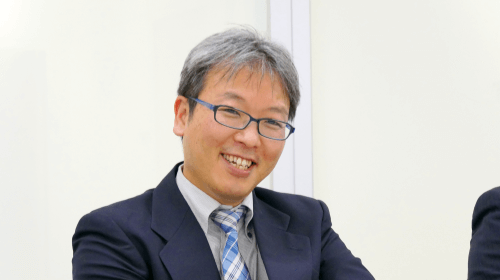
風に対する安全性を確保した上で、雨漏りのリスク回避という観点から、屋根上(防水層)への穴あけが不要、さらに置くだけで施工できることはマストでした。ところが市場に出ている置き基礎架台は、風に対する安全性が確保されているという確証がもてず、納得できるところまで自社で開発していこうという流れになったのです。
当社は地上設置においては、長年のノウハウとスキルがあります。しかし地中に杭を深く埋め固定する地上設置と異なり、今回の屋根上設置の架台は高い建物の上に設置することを想定します。万が一暴風が吹き荒れても、確実に飛ばない安全な架台でなくてはなりません。
「人命に関わることでもあり、我々には設計責任が生じます。やるなら慎重に、確実に飛ばないものでないと売らないという固い気持ちでスタートしました。」
当社は地上設置においては、長年のノウハウとスキルがあります。しかし地中に杭を深く埋め固定する地上設置と異なり、今回の屋根上設置の架台は高い建物の上に設置することを想定します。万が一暴風が吹き荒れても、確実に飛ばない安全な架台でなくてはなりません。
「人命に関わることでもあり、我々には設計責任が生じます。やるなら慎重に、確実に飛ばないものでないと売らないという固い気持ちでスタートしました。」
降りかかる課題に
どう向き合って
いくのか
いざ製品開発を開始すると、想定外の事態が発生しました。
土台となるベースレールは、アルミ外殻の内側にモルタルを充填して重さを出すのですが、モルタルがアルカリ性のため、ベースレールのアルミ外殻の腐食が発生することがわかりました。
そこでアルカリと反応しないように表面処理を施す必要性が生じたのですが、長い筒状のままだとアルミ外殻の内側にアルマイト処理を施すことができません。何度も試行錯誤した末、レールを縦に4分割すれば表面処理時の部材の外側と内側がなくなり、この問題を解決できることがわかったのです。
土台となるベースレールは、アルミ外殻の内側にモルタルを充填して重さを出すのですが、モルタルがアルカリ性のため、ベースレールのアルミ外殻の腐食が発生することがわかりました。
そこでアルカリと反応しないように表面処理を施す必要性が生じたのですが、長い筒状のままだとアルミ外殻の内側にアルマイト処理を施すことができません。何度も試行錯誤した末、レールを縦に4分割すれば表面処理時の部材の外側と内側がなくなり、この問題を解決できることがわかったのです。
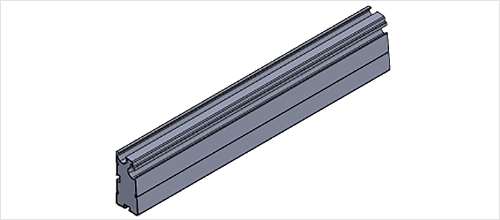
ベースレール ▲
「試作段階でうまくいったとしても、当然のことながら量産時に同じようにできないと意味がありません。量産先の海外工場では、日本で当たり前のことでも異なる可能性があります。そのような中で安価かつ、誰が作っても同じクオリティのものをラインに乗せられるよう、開発を進める必要がありました。」
2019年12月、試作品による初めての耐風速性能試験が実施されました。今回の試験では風速60m/sのクリアを目標としていました。
これまで何度も試行錯誤を繰り返し、完成した試作品。市場に出ている置き基礎架台より重い上に、太陽電池モジュールの裏面に風が入りにくい構造としているため、メンバーは当然のごとく大丈夫だろうと考えていました。
試験は台風直撃時の強風を再現する巨大な扇風機のような機械を用い、風速10m/sからスタート。順調に思えた矢先、風速40m/s※でUNIFIXは飛んでしまったのです。
「重量物が軽々と目の前で舞い上がってしまったときは衝撃でした。」
2019年12月、試作品による初めての耐風速性能試験が実施されました。今回の試験では風速60m/sのクリアを目標としていました。
これまで何度も試行錯誤を繰り返し、完成した試作品。市場に出ている置き基礎架台より重い上に、太陽電池モジュールの裏面に風が入りにくい構造としているため、メンバーは当然のごとく大丈夫だろうと考えていました。
試験は台風直撃時の強風を再現する巨大な扇風機のような機械を用い、風速10m/sからスタート。順調に思えた矢先、風速40m/s※でUNIFIXは飛んでしまったのです。
「重量物が軽々と目の前で舞い上がってしまったときは衝撃でした。」
※風速40m/sは何かにつかまらないと立っていられず、屋根瓦や看板が落下・飛散するほどの威力。
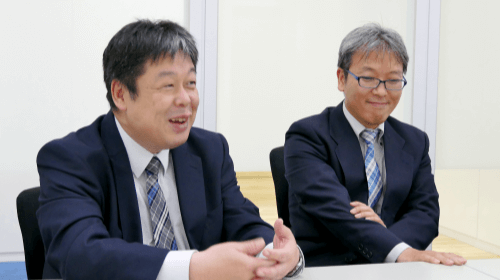
浮き上がった原因は、UNIFIXと地面の隙間に風が入り込むことでした。試験では単に「失敗だった」で終わるのではなく、次回に活かすための方向性だけでも見出す必要があります。意気消沈し頭を抱えるメンバーたち。その中で一人がひらめいたのです。
「下に風が入ることがダメなのであれば、風を受け流せば良いのでは。」その考えのもと、試験場近くのホームセンターである物を購入しました。それはなんと駐車場用のゴム製カースロープ。そのカースロープをUNIFIXの地面との隙間を埋めるような形で設置したのです。
すると思惑通り、スロープの形に沿って風が上へ流れることで、風速40m/s以上でも耐えられるようになりました。これはいけるかもしれない。光明を見出したメンバーは、再度試験に臨むため、最適な部材の開発へと乗り出したのです。
「下に風が入ることがダメなのであれば、風を受け流せば良いのでは。」その考えのもと、試験場近くのホームセンターである物を購入しました。それはなんと駐車場用のゴム製カースロープ。そのカースロープをUNIFIXの地面との隙間を埋めるような形で設置したのです。
すると思惑通り、スロープの形に沿って風が上へ流れることで、風速40m/s以上でも耐えられるようになりました。これはいけるかもしれない。光明を見出したメンバーは、再度試験に臨むため、最適な部材の開発へと乗り出したのです。
データが
何よりも強い、
安全性の証明となる
次回の試験は設備の都合上、一か月後の実施となりました。さらには年末年始を挟むスケジュールであったため、作業は急ピッチで進みました。カースロープの形状を重量のあるコンクリートで製作する必要があったのですが、コンクリートを流し込む型枠を製作している時間がありません。そこで、形状と重量を合わせれば、ひとまず試験は可能ということで、ベースレールと同様に金属外殻の内側にモルタルを充填する案を思いつきました。
「付き合いの深い板金屋さんに無理を言って、超短納期で作ってもらいました。これは日ごろの関係性のおかげですね。」
風を受け流すための部材は、ある程度の重量も必要ですが、施工性・安全性と両立させるために25g以下のものとなりました。こうして「整流ブロック」というUNIFIXをぐるりと取り囲む、風受け用の部材が完成したのです。
「付き合いの深い板金屋さんに無理を言って、超短納期で作ってもらいました。これは日ごろの関係性のおかげですね。」
風を受け流すための部材は、ある程度の重量も必要ですが、施工性・安全性と両立させるために25g以下のものとなりました。こうして「整流ブロック」というUNIFIXをぐるりと取り囲む、風受け用の部材が完成したのです。
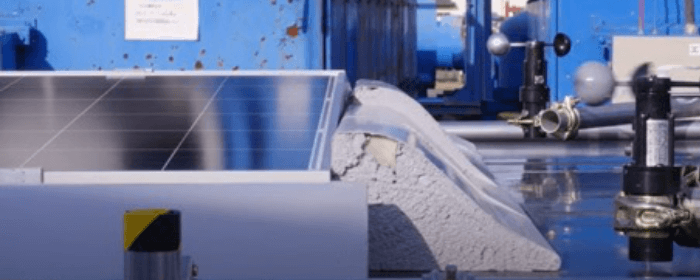
▲ 取り囲む「整流ブロック」
年が明けた2020年1月中旬、再試験が行われました。ここでは見事、実風速70m/s以上で、10秒以上の安定性をクリアし、UNIFIXの安全性を完全に証明することができました。長きに渡る苦労が報われた瞬間でもありました。
「事前にいくらシミュレーションをしても実際には想定外の事態が起こることも大いにあります。その時にその場で何ができるか、どう機転を利かすのかが勝負です。そして何より転んでしまっても必ず前を向いて立ち上がる不屈の精神を持つこと。ホームセンターが試験場の近くにあったのも幸運でした。」
「事前にいくらシミュレーションをしても実際には想定外の事態が起こることも大いにあります。その時にその場で何ができるか、どう機転を利かすのかが勝負です。そして何より転んでしまっても必ず前を向いて立ち上がる不屈の精神を持つこと。ホームセンターが試験場の近くにあったのも幸運でした。」
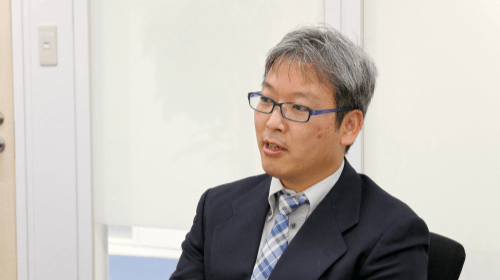
台風直撃でも飛ばない風への強さに加え、地震大国である日本において、いかに振れに強いかも重要視されます。そこで巨大地震時の屋上の揺れを再現した耐震性試験も実施しました。試験では、①塩ビシート ②ゴムシート ③ウレタン塗膜 ④コンクリート被覆の4つの屋上防水層パターンを想定。結果、塩ビシートとゴムシートの場合、標準仕様のままでも揺れに強く、ウレタン塗膜やコンクリート被覆では、滑り止めゴムシートをベースレールに貼り付けた耐震強化仕様にすれば良いことがわかりました。
また、UNIFIXが低重心かつ軽量であるため、地震の揺れでUNIFIXが滑動しても屋根の防水層をほとんど傷つけることがなく、屋上防水機能を維持できることも明らかになりました。
「想定値が一つもなく、実大モデル・実風速・実振動での試験結果があることこそ、UNIFIXの安全性を示す最大の武器となっています。」
また、UNIFIXが低重心かつ軽量であるため、地震の揺れでUNIFIXが滑動しても屋根の防水層をほとんど傷つけることがなく、屋上防水機能を維持できることも明らかになりました。
「想定値が一つもなく、実大モデル・実風速・実振動での試験結果があることこそ、UNIFIXの安全性を示す最大の武器となっています。」
止まることのない
進化
UNIFIXは実データで高い耐風・耐震安全性を証明できているため、設置条件を反映した細かい設計によって、安全性を確保する必要がありません。つまり誰が設置しても、一律で同じ水準の安全性を担保できるのです。
「固定しない、屋根に穴をあけなくていいということは建物の所有者にとってうれしいポイントです。さらに人力で持ち運びができるため工事の担当者もラクになります。またこれらの手軽さから販売店も売りやすい商品といえます。すべての関係者に何かしらメリットがあるのです。」
営業活動を進める中で、「工場は将来的に立てるしその土地もあるが、建設予定日はまだ決まっていない」という状況において、UNIFIXの利便性が非常に高いと評価を受けています。建設予定地の地面にUNIFIXを設置しそこで発電をし、工場が建ったら屋根上に移す、ということができるからです。
「固定しない、屋根に穴をあけなくていいということは建物の所有者にとってうれしいポイントです。さらに人力で持ち運びができるため工事の担当者もラクになります。またこれらの手軽さから販売店も売りやすい商品といえます。すべての関係者に何かしらメリットがあるのです。」
営業活動を進める中で、「工場は将来的に立てるしその土地もあるが、建設予定日はまだ決まっていない」という状況において、UNIFIXの利便性が非常に高いと評価を受けています。建設予定地の地面にUNIFIXを設置しそこで発電をし、工場が建ったら屋根上に移す、ということができるからです。
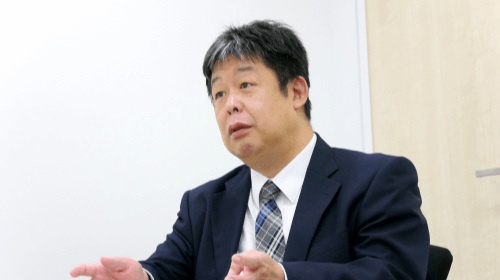
「施設も予算も人員も大手に比べたら乏しい中で、柔軟な対応力で大手に負けない成果を出す、当社の強みはここにあると思います。社会的なニーズの高まりもあり、UNIFIXは当初の想定した10倍ほどの販売量を見込んでいます。今後はそれに合わせて生産量を拡大させるとともに、大型化していく太陽電池モジュールに対応できるUNIFIXを開発することが目下の課題です。」